The rapier is a distant relative of the sword. But if the main purpose of the sword is to deliver chopping and, much less often, stabbing, then the rapier is a large needle, which is used to deliver exceptionally fast stabbing blows. For this purpose, it is made as light as possible and at the same time very durable in order to provide it with "punching" qualities.
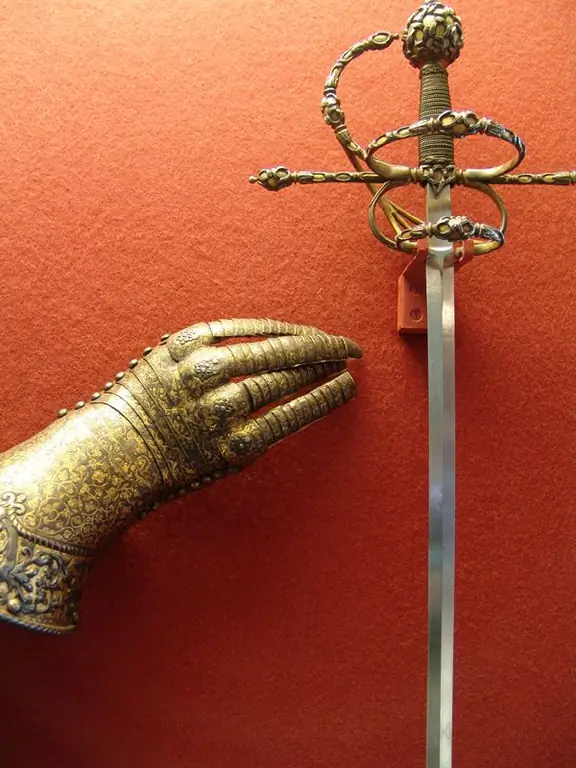
Instructions
Step 1
The rapier belongs to the category of bladed weapons, for the manufacture of which steel 65G and 60S2 with a high carbon content are used. The starting material for the rapier is a steel bar, consisting of seven bags. First, you forge a four-sided workpiece from it, so that there is a margin for forging and retracting the blade. It is worth recalling that the modern sports foil consists of two parts - the blade and the mount. The blade has a tetrahedral cross-section, thinned at the end. It is conventionally divided into three parts - more flexible, weak, medium and strong, thickened. Its length should not exceed 110 cm, and its weight should be half a kilogram.
Step 2
Then you proceed to forging valleys - special longitudinal grooves designed to facilitate the construction of a rapier. For hammer forging, a shperak is used - T-shaped tongs with round jaws. The workpiece takes on an almost finished shape after the blade is pulled back. This operation is quite complex and requires great precision and therefore must be done manually. At this stage, the rapier configuration is finally formed, after which you can proceed to heat treatment.
Step 3
To relieve internal stresses, the product is annealed at a temperature of 950-970 degrees C, and then it is cooled directly in the furnace for 5-8 hours. After heat treatment, the blade should be carefully inspected for cracks and other defects. For greater persuasiveness, you should hit them hard flat on the board.
Step 4
The final stage is mechanical processing with the help of moistened abrasive sandstone stones, during which excess metal is removed, the valleys are polished, the piercing edge is formed and sharpened. This can take up to two weeks.
Step 5
The final check consists of an external examination and control injections. The made rapier should be bent and released sharply. If the rapier is perfectly straightened, then your work was not in vain.