Boarding is not only a great way to relax and recharge, but also a popular applied sport. Modern skateboarders are able to perform amazing pirouettes, delighting the audience and skate fans. To make riding on the board comfortable and safe, the skate is made in compliance with all the intricacies of technology.
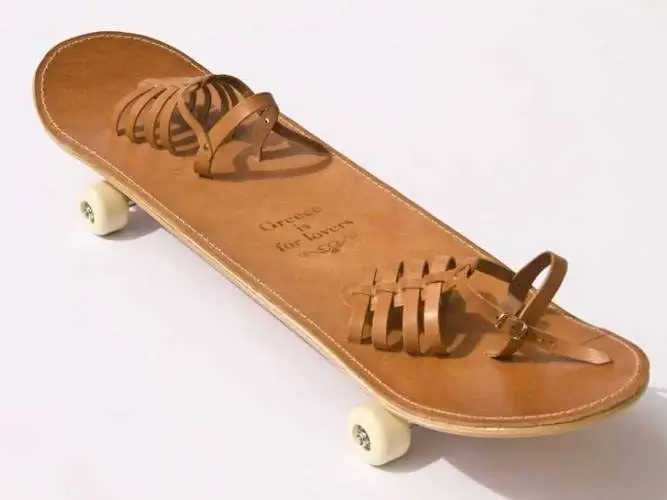
Instructions
Step 1
Traditionally, skateboards are made from several layers of durable wood or plywood. The more expensive a sports equipment is, the better the materials used for its manufacture. The best examples of boards are made from six to seven layers of maple plywood with the obligatory facing of the ends.
Step 2
The production process for the mass production of skateboards is divided into several successive stages. Several layers of plywood are installed on a special rack, between which a special adhesive is applied. The adhesive used to make the boards is able to withstand strong shocks and prolonged vibration.
Step 3
Then the assembled pack is placed in a mold corresponding in size and configuration to the future skateboard. The press exerts a pressure of several tens of tons on the material. At the same time, plywood sheets are squeezed, forming a single whole. Excess adhesive flows down the edges of the pack, which at the same time forms an even more monolithic mass. The finished block is left in this state for several hours.
Step 4
The next step is to drill holes for the front and rear tracks, which will rotate on their axis, allowing the board to turn in the desired direction.
Step 5
Only now the block of rectangular shape is given the familiar outlines of a skateboard. For this, several types of templates are used, taking into account the configuration of a particular model. After applying the template and processing with a milling cutter, the skate takes on a familiar look.
Step 6
The stage of surface grinding begins. After processing on a grinding machine, the future skate is polished using a set of brushes and different types of sandpaper. The task at this stage is simple, but crucial - to remove the rough wood fibers to make the skate perfectly smooth.
Step 7
Now the product goes to the finishing workshop, where the board is covered with a primer and a layer of colorless varnish. If necessary, a pattern is applied to the top surface of the skate. After the protective coating has completely dried, the chassis is mounted on the skate. The board is now completely ready to use.